High Pressure Plunger pumps are used in a variety of applications. They are available in a variety of styles and materials, including cast iron and aluminum. In addition, some models have a brass nickel plated head for added strength under high pressure. When choosing a High Pressure Plunger pump, consider the environment it will be used in before deciding on the material for the cylinder head.
High-pressure plunger pumps
High-pressure plunger pumps are widely used in industrial cleaning, truck wash, and sewer cleaning applications. They can pump liquid media up to hundreds of gallons per minute. Some plunger pumps can operate up to 200 psi, while others can reach more than 20,000 psi for water blasting.
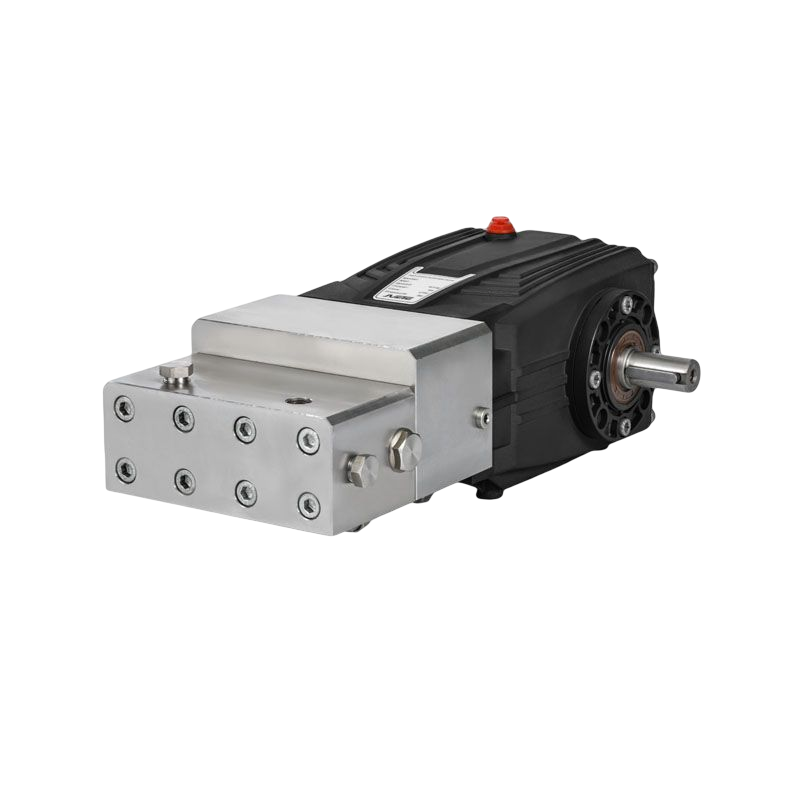
Plunger pumps are typically made from high pressure plunger pumps suppliers forged steel or a steel alloy. The latest models are equipped with variable-speed drives that reduce energy consumption while maintaining pump performance. KAMAT has introduced a new powertrain in their high-pressure plunger pumps that makes them easier to use, quieter, and more efficient than previous models.
Reciprocating
Reciprocating high pressure plunger pumps are designed to handle varying pressures without the need for speed adjustment. The pumps are also capable of handling significant volumes of gas or vapour. The pumps utilize three types of mechanisms: the piston, plunger, and diaphragm. The pumps are constructed to operate in a continuous duty cycle over a 20-year design life. These pumps are available in different configurations to fit the needs of various applications. They are ideal for pumping abrasive slurries and high viscosity liquids.
The principle behind reciprocating high pressure plunger pumps is simple: the pump plunger is connected to a crankshaft through a connecting rod. A motor attached to the crankshaft converts the rotary motion of the plunger to a reciprocating motion. The power delivered to the plunger via the connecting rod moves the plunger upwards and downwards inside the cylinder. As the pump moves upward and downwards, it creates a vacuum inside the pump chamber, which reduces the pressure difference between the fluid inside the cylinder and the external pressure.
Filter system
High-pressure plunger pumps are a great choice when you need high-pressure pumping. These pumps have several benefits, and are available in a variety of materials. They can achieve pressure stages of up to 3,000 bar. Some are available with different plunger and seal packages for optimal pressure and flow. They also come with high-strength ductile iron cylinders and aluminum-bronzed cylinder bodies.
Several features are important to consider when selecting a filter system for a high-pressure plunger pump. First, consider your pump's application. The design should meet the specifications of the application. It should be mounted in a location away from direct spray or splashes. Additionally, it should be mounted on a horizontal, rigid surface. Furthermore, it should not be stored in a high-temperature area without proper ventilation. A solid ceramic plunger offers the highest resistance to corrosion and abrasion, and will increase pump seal life.
Manifold seals
Performing a repair on manifold seals of high pressure plunger pumps involves careful work. These seals are vulnerable to accelerated wear and tear, particularly those that are found in the intake and discharge valves. In order to properly replace them, you should follow a few simple steps.
Suction manifolds are commonly available and are made from standard steel "TEE" pipe fittings. These fittings are formed with generous radii at the intersection. The radii must be evenly spaced in order to prevent leakage of fluid.
Compact power transmission
High-pressure plunger pumps are designed for transferring hydrocarbon at high pressures and flow rates. These pumps are ideal for oil and gas industries and can be found in a wide range of sizes. They are also used for conveying water during refinement and production. Compact power transmission is necessary for high-pressure plunger pumps.
Compact power transmission reduces noise and increases energy efficiency. KAMAT engineers have developed split gear cases to transmit power to the plunger. This design also contributes to the increased running smoothness and reduced noise of these pumps. The company also owns all driveline components and developed them in-house.
Applications
High pressure plunger pumps have a wide range of applications. They are ideal for moving high-viscosity or heavy substances. However, their operation and maintenance costs are high. In addition, they cannot deliver free flowing or pulsating fluids. However, their versatility makes them the perfect choice for various processes.
The type of material used in high-pressure plunger pumps depends on the application. The base (casing) and cylinder should be corrosion-resistant. Materials used to make the plunger, discharge valves and suction valves must be abrasion and chemical-resistant. High-pressure plunger pumps can be made from cast iron or steel. Cast iron offers good tensile strength, durability and abrasion resistance. Compared to cast iron, plastics offer a wide range of chemical resistance. Similarly, steel alloys offer excellent corrosion resistance.