Working principle of high pressure plunger pump
The high-pressure plunger pump is a kind of reciprocating pump, which belongs to the volume pump. The plunger is driven by the eccentric rotation of the pump shaft and reciprocates. When the plunger is pulled out, the pressure in the working chamber decreases and the outlet valve closes. When it is lower than the inlet pressure, the inlet valve opens and the liquid enters; when the plunger is pushed inward, the working chamber pressure rises and the inlet valve closes. The outlet valve opens and the liquid drains.
The axial piston pump with high pressure plunger pumps manufacturer sliding shoe structure is the most widely used axial piston pump at present. The piston placed in the cylinder body is in contact with the swash plate through the sliding shoe. When the drive shaft drives the cylinder body to rotate, the swash plate Pull the plunger out of the cylinder or push it back to complete the oil suction and discharge process. The oil in the working chamber formed by the plunger and the cylinder hole is communicated with the suction and discharge chambers of the pump respectively through the oil distribution plate. The variable mechanism is used to change the inclination of the swash plate, and the displacement of the pump can be changed by adjusting the inclination of the swash plate.
Maintenance of high pressure plunger pump
The swash plate axial piston pump generally adopts the form of cylinder rotation and end face distribution. The end face of the cylinder body is inlaid with a friction pair composed of a bimetallic plate and a steel oil distribution plate, and most of them adopt the method of plane distribution, so the maintenance is more convenient. The oil distribution plate is one of the key components of the axial piston pump. When the pump is working, on the one hand, the high-pressure oil in the working chamber pushes the cylinder body to the oil distribution plate, and on the other hand, the oil film pressure between the oil distribution plate and the cylinder body forms a pair of pressures. The hydraulic reverse thrust of the cylinder pushes the cylinder away from the oil distribution pan. The designed hydraulic pressing force Fn of the cylinder block to the oil distribution plate is slightly larger than the hydraulic reverse thrust Ff of the oil distribution plate to the cylinder block, that is, Fn/Ff=1.05~1.1, so that the pump works normally and maintains a high volumetric efficiency.
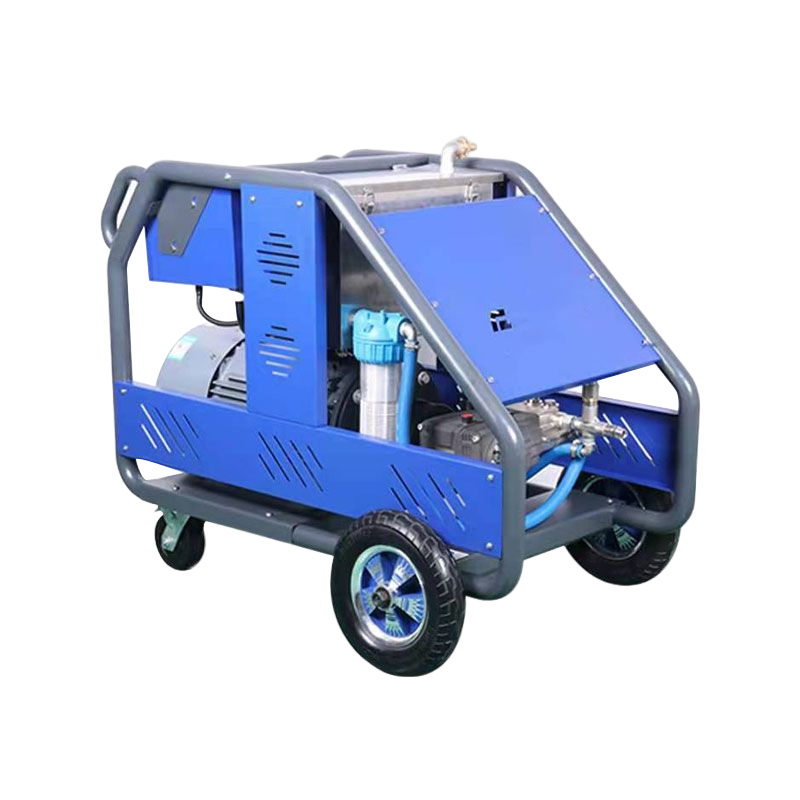
In fact, due to the contamination of the oil, there is often slight wear between the oil distribution plate and the cylinder block. Especially at high pressure, even slight wear can increase the hydraulic reverse thrust Ff, thereby destroying Fn
There are many manufacturers producing plunger pumps now, and the structures of imported and domestic parts are different. Each pump should be used in strict accordance with its factory instruction manual. When repairing the pump, you should first check whether the pump is installed and used properly in the system, so as to find out the cause of damage in time, eliminate hidden dangers, and ensure the normal operation of the system. The repaired hydraulic pump should be tested by certain testing equipment before it can be used. If it does not have the detection conditions, it should also be repeatedly debugged in the system to make it work normally.